Technician Time Management:
Maximize Efficiency with Shopwatch
What is Shopwatch?
Squarerigger’s Shopwatch is a real-time technician tracking feature that helps repair shops monitor time spent on tasks, reduce inefficiencies, and optimize labor allocation. By automatically capturing work time, managers gain full visibility into technician productivity, ensuring jobs are assigned efficiently, training is targeted, and wrench time is maximized.
How Shopwatch Optimizes Shop Productivity
Many shops struggle with tracking technician efficiency, identifying time waste, and ensuring fair labor distribution. Shopwatch solves these challenges by giving managers clear insights into work time, ancillary tasks, and technician performance trends, helping businesses improve repair timelines and reduce costs.
Benefits of Squarerigger’s Shopwatch Time Management
- Eliminate Manual Time Tracking: Easily record work hours for accurate labor cost calculations.
- Optimize Technician Assignments: Use data to match the right techs to the right jobs, improving efficiency.
- Increase Accountability & Team Collaboration: Track who's working on what and ensure fair labor distribution.
- Reduce Shop Inefficiencies: Identify idle time, bottlenecks, and areas for workflow improvement.
- Boost Profitability: Ensure billable hours are captured, and technicians stay focused on revenue-driving tasks.
- Estimated Repair Times: Ensure profitability on each job based on your historical repair time data. More accurately estimate labor for recurring repairs.
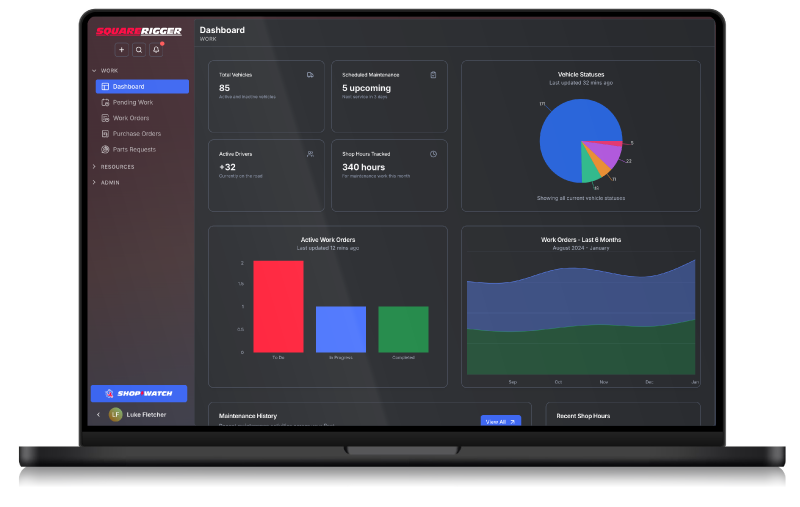
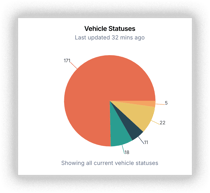
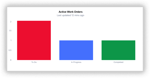
Key Features of Shopwatch
-
Real-Time Technician Time Tracking
- Technicians clock in and out of tasks directly from Squarerigger’s interface on any device.
- Capture time spent on work orders, diagnostics, and indirect shop tasks.
- View live timers for ongoing jobs to monitor progress at a glance.
-
Automated Reporting & Labor Analysis
- Generate reports on task-specific efficiency, comparing technician performance.
- Identify which technicians complete jobs faster and with higher accuracy.
- Optimize labor costs by assigning tasks based on individual strengths.
-
Maximize Wrench Time & Reduce Idle Time
- Track how much time is spent on actual repairs vs. non-billable activities.
- Identify bottlenecks in the repair process and streamline operations.
- Ensure technicians are spending time on revenue-generating work.
-
Seamless Work Order Integration
- Attach technician time logs directly to work orders for accurate cost tracking.
- Ensure labor charges are properly billed without guesswork.
- Improve maintenance forecasting and workload balancing.
How Shopwatch Helps Fleet Repair Shops
Without an accurate time tracking system, fleet repair shops lose visibility into technician productivity, labor costs, and inefficiencies. Shopwatch provides the data needed to fine-tune operations, improve turnaround times, and maximize labor profitability.
How Technician Time Tracking Impacts Shop Efficiency
When repair shops don’t track technician time accurately, productivity suffers. Technicians may spend more time than necessary on tasks, high-performing techs can go unrecognized, and training opportunities are missed. Without visibility, shop managers struggle to make data-driven decisions about labor allocation and process improvements.
Pain Point: Untracked Time and Inefficient Labor Allocation
Without a structured time management system, shops face:
- Low Wrench Time: Too much technician time is spent on non-repair tasks or waiting on parts, bays, or approvals.
- Lack of Visibility: Managers can’t see how long tasks are actually taking or identify which techs are most efficient.
- Inconsistent Job Costing: Without accurate labor tracking, estimating and billing become guesswork.
- Missed Training Opportunities: Shops have no way to identify skill gaps or assign techs to tasks based on strengths.
- Technician Burnout or Underperformance: Unbalanced workloads and lack of recognition can lead to dissatisfaction and turnover.
Solution: Technician Time Management with Shopwatch
Squarerigger’s Shopwatch feature tracks technician time on each task in real-time—giving shops the data they need to increase productivity, improve job assignments, and reduce wasted time.
- Clock-In / Clock-Out by Task: Techs log time directly on each job or task using any device.
- Real-Time Job Tracking: See which techs are working on which tasks, how long each task is taking, and where bottlenecks are happening.
- Task-Based Efficiency Reporting: Identify which technicians are most efficient at specific jobs and adjust assignments accordingly.
- Training Insights: Use time data to identify where additional training or support may improve task completion rates.
- Labor Accuracy: Improve job costing and billing accuracy by capturing actual labor time per job.
End Result: Maximize Wrench Time & Optimize Shop Labor
By using Shopwatch for technician time management, shops gain: - Higher Productivity: Identify and reduce unproductive time to keep techs focused on repair work.
- Smarter Scheduling: Assign jobs based on real efficiency data, not guesswork.
- Accurate Job Costing: Track labor time per task for precise billing and profitability.
- Improved Training & Retention: Spot trends in tech performance and provide targeted support.
- More Balanced Workloads: Ensure tasks are distributed fairly, improving morale and reducing burnout.
Take Control of Technician Time with Shopwatch
With Squarerigger’s Shopwatch, fleet managers and repair shops gain real-time visibility into labor efficiency, ensuring technicians stay productive, jobs are completed on time, and profitability is maximized.
📅 Get a demo today to see how Shopwatch can streamline your shop’s operations!
Frequently Asked Questions
Have questions? We’ve got answers. See how Squarerigger helps fleets optimize operations, reduce costs, and improve efficiency.
-
Q: How does Shopwatch track technician time?
A: Technicians clock in and out of specific jobs or tasks, and Shopwatch automatically records work durations for accurate labor tracking.
-
Q: Can Shopwatch help identify technician strengths?
A: Yes! The reporting tools allow managers to see which techs complete jobs efficiently, making it easier to assign tasks based on skillset.
-
Q: How does Shopwatch integrate with work orders?
A: Technician time logs attach directly to work orders, ensuring labor costs are recorded accurately and billing is precise.
Check Out More of Our Shop Management Software Features
Purchasing Management
Squarerigger streamlines PO creation, vendor tracking, and real-time reporting, ensuring cost control and procurement efficiency to reduce or eliminate overspending and stock shortages.
Read MoreInventory Management
Squarerigger provides real-time tracking, barcode scanning, and automated stock level alerts, ensuring a streamlined and cost-effective inventory management process.
Read MoreMulti-Shop Management
Squarerigger offers centralized control, real-time reporting, and multi-location resource sharing, ensuring scalability and operational efficiency for repair shops with multiple locations.
Read More