Fleet Inspections: Ensure Safety, Compliance & Fleet Reliability
What Are Fleet Inspections?
Fleet inspections are critical to ensuring vehicle safety, regulatory compliance, and operational efficiency. They help identify potential issues before they escalate into costly breakdowns or compliance violations. From daily pre- and post-trip inspections to scheduled in-depth assessments, a well-structured inspection program keeps your fleet in peak condition. .
How Squarerigger’s Inspection Tools Keep Your Fleet Safe & Compliant
Squarerigger simplifies fleet inspections by providing digital, customizable checklists, automated tracking, and seamless integration with work orders. Our inspection management tools help fleet managers ensure that every vehicle meets safety and compliance requirements — without the hassle of paperwork.
Beyond compliance, Squarerigger enhances accountability and teamwork within your fleet. When a driver reports an issue during an inspection, a work request is automatically generated, ensuring that the necessary repairs are assigned and tracked. This process holds the shop accountable for completing repairs while reinforcing the importance of thorough inspections for drivers.
By creating a culture of accountability, drivers are more likely to perform inspections diligently, knowing their concerns will be addressed. In turn, technicians have clear visibility into repair priorities, ensuring issues don’t fall through the cracks—leading to a safer, more efficient fleet.
Benefits of Squarerigger’s Inspection Management Solution
- Ensure Fleet Safety – Identify potential hazards before they become serious issues.
- Reduce Repair Costs – Catch minor problems early to prevent expensive repairs.
- Minimize Downtime – Automate work requests for failed inspection items and keep vehicles on the road.
- Simplify Compliance – Maintain digital records to meet federal, state, and industry regulations.
- Improve Efficiency – Eliminate paperwork and streamline inspection reporting.
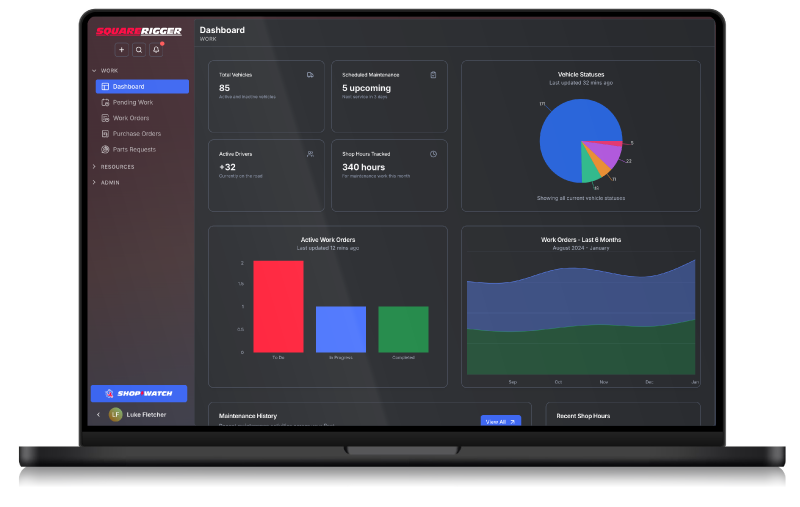
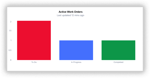
Key Features of Squarerigger’s Inspection Management
-
Pre- and Post-Trip Inspections
- Drivers complete daily inspections before hitting the road and after returning to the yard.
- Checklists cover lights, brakes, tires, fluid levels, leaks, hoses, mirrors, body damage, etc.
- Digital logs ensure compliance with Driver Vehicle Inspection Reports (DVIRs) and regulatory requirements.
-
Customizable Inspection Checklists
- Tailor inspection templates to match your fleet’s unique requirements.
- Set mandatory fields to ensure key safety components are always reviewed.
- Standardize inspection processes across all vehicles and asset types.
-
Automated Work Order Creation
- Failed inspection items automatically generate work requests, reducing downtime.
- Connect inspections directly to maintenance workflows to ensure immediate action.
- Track outstanding issues and repair status in real-time.
-
Paperless Digital Inspections
- Drivers and technicians complete inspections from any device—no clipboards needed.
- Inspection reports are uploaded instantly, eliminating lost or incomplete paperwork.
- Secure, cloud-based storage ensures records are accessible for audits and compliance.
-
Scheduling & Compliance Tracking
- Set up automated reminders for monthly, quarterly, and annual inspections.
- Maintain compliance with DOT, OSHA, and FMCSA regulations with accurate record-keeping.
- Quickly access historical inspection data for audits, fleet performance analysis, or warranty claims.
How Inspections Impact Fleet Efficiency & Cost Control
Regular fleet inspections play a crucial role in maintaining vehicle safety, ensuring compliance, and minimizing unexpected downtime. However, many fleets struggle with manual inspection processes that lead to incomplete reports, lost documentation, and delayed repairs. These inefficiencies not only increase operational costs but also put fleet reliability and driver safety at risk.
Pain Point: The Cost of Incomplete or Inconsistent Inspections
Without a structured, automated inspection process, fleets often face:
- Elevated Repair Expenses: Emergency repairs often incur higher costs due to expedited services and potential overtime labor charges.
- Compliance Risks: Missing, incomplete, or inaccurate inspection reports can lead to failed audits and costly fines.
- Unplanned Downtime: Issues that go undetected escalate into breakdowns, costly repairs, and service delays.
- Lack of Accountability: Without real-time tracking and automated work orders, inspection failures may go unresolved, leading to repeat failures and safety concerns.
- Paper-Based Inefficiencies: Manual inspection logs are time-consuming, prone to human error, and difficult to organize for audits and compliance tracking.
- Legal Liability Risks: In the event of an accident, incomplete or missing inspection records can expose your fleet to legal action and nuclear verdicts. Detailed, time-stamped inspection documentation helps prove that a vehicle was properly maintained and safe to operate—critical for protecting your drivers, your company, and your reputation.
Solution: Pro Digital, Automated Inspections with SquareriggerSquarerigger
Squarerigger’s PM solution offers a proactive approach by:
- Customizable digital inspection checklists to fit fleet-specific compliance needs.
- Automated work request creation for failed inspection items, ensuring immediate action.
- Real-time tracking and historical records to maintain audit readiness.
- Seamless mobile access, allowing drivers and technicians to perform inspections from any device.
End Result: A Safer, More Reliable Fleet
By implementing Squarerigger’s Inspection Management tools, fleets experience: - Improved Compliance: Reduce audit risks with accurate, digital records and automated reporting.
- Lower Repair Costs: Address minor issues before they escalate into major repairs.
- Reduced Downtime: Keep vehicles on the road and operating efficiently with proactive maintenance workflows.
- Stronger Accountability: Ensure drivers complete thorough inspections and technicians prioritize necessary repairs.
- Increased Safety & Efficiency: A fully integrated system that ensures fleet managers, drivers, and technicians stay connected for smarter decision-making.
Routine inspections are the first line of defense against unexpected breakdowns, compliance violations, and unnecessary downtime. Squarerigger’s inspection tools give fleet managers the visibility and automation needed to ensure every vehicle is road-ready, every day.
Pre- and Post-Trip Inspection Checklists
A well-structured inspection process ensures your fleet is operating safely and efficiently. Below are recommended pre- and post-trip inspection checklists that fleet managers can use as a foundation when setting up custom digital inspections in Squarerigger.
Pre-Trip Inspection
Before hitting the road, drivers should check:
✅ Tires – Pressure, tread depth, and overall condition.
✅ Brakes – Functionality, brake pads, and fluid levels.
✅ Lights – Headlights, brake lights, turn signals, and hazard lights.
✅ Fluids – Oil, coolant, windshield wiper, and brake fluid levels.
✅ Cargo – Properly secured loads and balanced weight distribution.
✅ Windshield & Mirrors – Clean and free of obstructions.
✅ Emergency Equipment – Safety kits, fire extinguishers, and warning triangles.
✅ Exterior Condition – Visible damage, leaks, or loose components.
✅ Route & Weather – Review conditions and adjust plans accordingly.
Post-Trip Inspection
At the end of each trip, drivers should inspect:
✅ Exterior Check – New dents, scratches, or signs of damage.
✅ Tires – Punctures, abnormal wear, or pressure issues.
✅ Cargo Area – Secure cargo, identify shifts or damage.
✅ Fluids – Check for leaks or spills.
✅ Interior & Controls – Ensure all controls, gauges, and instruments are functioning.
✅ Documentation – Record mileage, fuel levels, and any incident notes.
✅ Maintenance Flags – Identify any issues requiring follow-up service.
Frequently Asked Questions
Have questions? We’ve got answers. See how Squarerigger helps fleets optimize operations, reduce costs, and improve efficiency.
-
Q: What is a fleet inspection?
A: A fleet inspection is a routine check of a vehicle’s condition to ensure it is safe, compliant, and road-ready. Inspections can be performed daily (pre- and post-trip), monthly, or at scheduled maintenance intervals to identify potential issues before they lead to costly repairs or downtime.
-
Q: How do pre- and post-trip inspections help fleet safety?
A: Daily inspections allow drivers to identify issues before they hit the road, preventing breakdowns and improving safety for everyone.
-
Q: Can Squarerigger’s inspections be customized for different vehicle types?
A: Yes! You can create custom checklists based on asset type, fleet needs, and compliance requirements.
-
Q: What happens when an inspection fails?
A: Failed items automatically generate work requests, ensuring repairs are logged and addressed without delays.
Check Out More of Our Fleet Maintenance Software Features
Work Order Management
Squarerigger’s work order management system provides the tools you need to standardize processes, eliminate inefficiencies, and ensure every repair is tracked, completed, and billed accurately.
Read MorePreventive Maintenance
Squarerigger’s preventive maintenance software is designed to help Fleet Managers stay ahead of costly repairs, reduce downtime, and extend the life of their vehicles and equipment.
Read MoreOutside Work
Squarerigger provides a centralized platform to manage external service providers, helping you maintain accurate records, control costs, and ensure timely repairs.
Read More