Work Order Management: Boost Technician Productivity & Reduce Downtime
What is Work Order Management?
Work order management is the backbone of an efficient fleet maintenance operation. It involves tracking, scheduling, and executing repair and service tasks to ensure all maintenance activities are properly documented, completed on time, and cost-controlled. A well-structured work order system improves workflow efficiency, reduces downtime, and enhances cost control.
How Work Order Management Helps Your Fleet Run Smoother
A disorganized maintenance workflow can lead to costly delays and mismanaged repairs. Squarerigger’s work order management system provides the tools you need to standardize processes, eliminate inefficiencies, and ensure every repair is tracked, completed, and billed accurately.
Benefits of Squarerigger’s Work Order Management Solution
Without structured work order management, fleets risk delayed repairs, lost productivity, and uncontrolled expenses. Squarerigger provides a centralized, automated approach to maintenance tracking, resulting in:
- Minimize Downtime – Keep vehicles on the road by streamlining service workflows and preventing unnecessary delays.
- Increase Shop Efficiency – Ensure technicians stay productive with optimized job assignments and time tracking for each job.
- Improve Cost Accuracy – Track labor, parts, and vendor expenses to get a true picture of repair costs.
- Enhance Compliance & Record-Keeping – Maintain digital service records for audits, warranties, and preventive maintenance tracking.
- Boost Productivity with Automation – Reduce manual entry and streamline approvals, job tracking, and reporting.
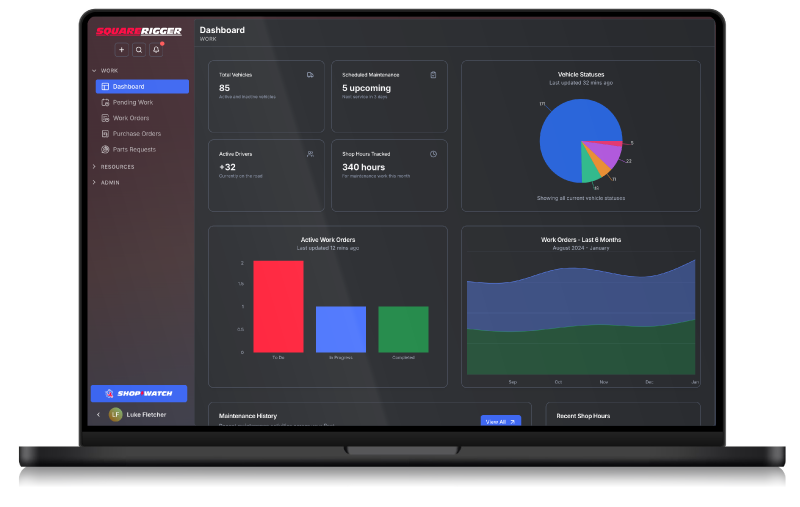
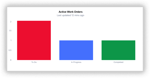
Key Features of Work Order Management with Squarerigger
Lorem ipsum dolor sit amet, consectetur adipiscing elit.
-
Fast & Easy Work Order Creation
- Generate work orders quickly, from any device, for scheduled maintenance, inspections, or unexpected repairs.
- Assign multiple services to a single work order, allowing for bundled maintenance tasks.
- Automatically link work requests and inspections to work orders for seamless tracking.
- Generate work orders from diagnostic trouble codes (DTCs) and mileage-based service needs with our telematics integrations.
-
Technician Assignment & Time Tracking
- Assign work orders to specific technicians based on availability, skillset, or priority level.
- Track labor hours with clock-in/clock-out functionality.
- Maximize wrench time by reducing administrative overhead and optimizing schedules.
-
Parts & Inventory Management
- Link parts directly to work order services, ensuring accurate usage tracking and cost allocation.
- View real-time inventory availability and create purchase orders with a click.
- Ensure you have the parts you need when you need them with barcode scanning and min/max inventory level notifications.
-
Mobile Accessibility & Digital Documentation
- Technicians can update work orders, log labor hours, and attach notes or images directly from any device.
- Drivers can report issues during pre- and post-trip inspections, triggering work order creation.
- Digitally capture inspection results, before/after repair photos, and warranty claims.
- Eliminate paperwork and maintain a centralized digital service history for every asset.
-
Cost Control & Reporting
- Automatically calculate labor, parts, and outside service costs for each work order.
- Gain insights with detailed cost breakdowns and fleet performance analytics.
- Improve budgeting and forecasting by identifying maintenance trends and cost-saving opportunities.
-
Maintenance Planning & Resource Optimization
- Use PM insights to plan resource allocation, technician schedules, and parts availability.
- Streamline maintenance workflows to reduce repair costs and improve shop productivity.
Smarter Work Order Management for Faster, More Efficient Repairs
A well-structured work order management system is the foundation of an efficient fleet maintenance operation. Without clear workflows and real-time tracking, repairs can be delayed, costs can spiral, and technicians may struggle to stay productive. Squarerigger’s work order management solution centralizes maintenance workflows, optimizes labor allocation, and ensures all repairs are completed on time—maximizing uptime and minimizing unnecessary expenses.
Unstructured work order processes lead to inefficiencies, unnecessary costs, and prolonged vehicle downtime. Whether it’s a missed repair, an unassigned technician, or inaccurate parts tracking, poor work order management can cause fleets to waste time and money.
Pain Point: Disorganized Workflows and Costly Repairs
Without a work order management system, fleets often face:
- Untracked Maintenance Costs – Poor visibility into labor, parts, and vendor expenses makes it difficult to control budgets.
- Delayed Repairs & Downtime – Lack of structured workflows means repairs can be overlooked or take longer than necessary.
- Inefficient Labor Use – Without clear job assignments and time tracking, technician productivity suffers, leading to lower wrench time and higher costs.
- Manual Data Entry & Lost Information – Relying on paper or spreadsheets leads to errors, lost work orders, and compliance issues.
Solution: Streamlined Work Order Management with Squarerigger
Squarerigger optimizes work order processes by:
- Automating Work Order Creation – Quickly generate, assign, and track maintenance tasks in one centralized system.
- Enhancing Technician Productivity – Assign work orders based on availability and expertise, while tracking labor hours for accurate job costing.
- Seamlessly Linking to Parts & Inventory – Ensure all required parts are available before work begins, reducing unnecessary delays.
- Digitizing the Maintenance Process – Provide technicians with mobile access to work orders, allowing for real-time updates, photo attachments, and instant documentation.
End Result: Increased Efficiency and Lower Costs
By leveraging Squarerigger’s Work Order Management tools, fleets can:
-
Reduce Downtime – Vehicles stay on the road longer with faster, more organized repairs.
-
Lower Maintenance Costs – Accurate tracking prevents unnecessary spending and ensures budget adherence.
-
Boost Technician Productivity – Assign the right jobs to the right people while tracking performance metrics.
-
Improve Decision-Making – Real-time data and reports provide insights into labor efficiency, asset performance, and maintenance costs.
Efficient work order management is key to running a profitable fleet operation. With Squarerigger, you gain full visibility into your maintenance workflow, ensuring faster repairs, reduced costs, and optimized technician performance. Our intuitive fleet maintenance platform ensures fleet managers, technicians, and shop personnel stay connected, organized, and focused on keeping vehicles on the road.
Frequently Asked Questions
Have questions? We’ve got answers. See how Squarerigger helps fleets optimize operations, reduce costs, and improve efficiency.
-
Q: How does Squarerigger’s work order system help reduce downtime?
A: By centralizing scheduling, technician assignments, and parts management, Squarerigger ensures repairs are completed efficiently, minimizing vehicle downtime.
-
Q: Can technicians update work orders in real time?
A: Yes! Squarerigger’s mobile-friendly interface allows technicians to log work, update statuses, and attach notes or images from any device.
-
Q: How does work order management improve cost control?
A: Squarerigger tracks labor, parts, and vendor costs per work order, providing detailed reporting to help control expenses and improve budgeting.
Check Out More of Our Fleet Maintenance Software Features
Preventive Maintenance
Squarerigger’s preventive maintenance software is designed to help Fleet Managers stay ahead of costly repairs, reduce downtime, and extend the life of their vehicles and equipment.
Read MoreInspections
Squarerigger's inspection management tools help fleet managers ensure that every vehicle meets safety and compliance requirements, without the hassle of paperwork.
Read MoreOutside Work
Squarerigger provides a centralized platform to manage external service providers, helping you maintain accurate records, control costs, and ensure timely repairs.
Read More