Lifecycle Management (TCO): Optimize Fleet Costs & Asset Longevity
What is Lifecycle Management & Total Cost of Ownership (TCO)?
Lifecycle management involves tracking the full financial impact of owning and operating fleet assets, from acquisition to disposal. Total Cost of Ownership (TCO) considers purchase costs, maintenance expenses, depreciation, and resale value, giving fleet managers data-driven insights to optimize replacement cycles and control costs.
How Squarerigger’s Lifecycle Management Tools Improve Fleet Operations
Squarerigger’s Lifecycle Management (TCO) solution helps fleets make smarter financial and operational decisions by analyzing costs, tracking asset health, and predicting optimal replacement timelines. With real-time data, you can maximize asset utilization, minimize unnecessary repairs, and strategically manage fleet investments.
Benefits of Squarerigger’s Lifecycle Management Solution
- Reduce Long-Term Fleet Costs: Optimize spending by tracking TCO and replacing assets at the right time.
- Maximize Asset Lifespan: Prevent premature replacements by maintaining assets effectively.
- Improve Budgeting & Forecasting: Gain data-driven insights for more accurate fleet financial planning.
- Optimize Fleet Size: Identify underutilized vehicles and avoid unnecessary acquisitions.
- Enhance Decision-Making: Compare repair vs. replacement costs for smarter asset management.
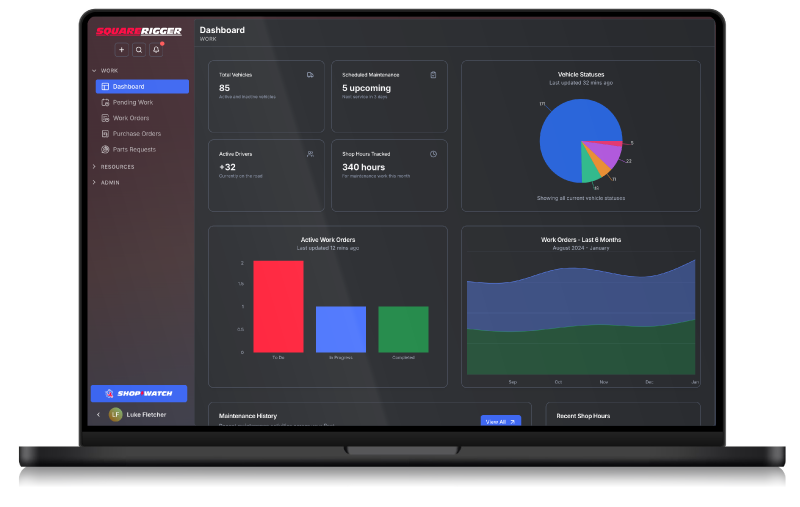
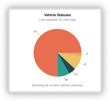
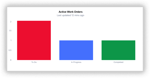
Key Features of Lifecycle Management (TCO) with Squarerigger
-
Complete Lifecycle Cost Tracking
- Monitor acquisition costs, financing, fuel, maintenance, repairs, and depreciation.
- Track asset value over time to determine when a vehicle becomes too costly to maintain.
- Understand total fleet operating expenses at both the asset and fleet-wide level.
-
Asset Utilization & Replacement Planning
- Identify underutilized or high-cost assets to optimize fleet size and usage.
- Forecast optimal replacement timing based on cost per mile/hour, repair frequency, and depreciation trends.
- Reduce unnecessary capital expenditures by extending asset lifespan through proactive maintenance.
-
Maintenance vs. Replacement Decision Support
- Compare ongoing maintenance costs to the cost of replacing an asset.
- Generate reports to determine whether keeping or replacing a vehicle is the most cost-effective option.
- Identify trends in repair frequency and downtime to support replacement planning.
-
Fleet-Wide Cost Analysis & Reporting
- Generate customizable TCO reports for budgeting, forecasting, and financial planning.
- View breakdowns of fleet operating costs by asset type, service category, or department.
- Gain actionable insights into where your fleet is overspending and where you can cut costs.
-
Integration with Maintenance & Procurement
- Link TCO data with work order management to analyze repair histories and costs.
- Track procurement trends and resale values to determine the best time to retire an asset.
- Ensure purchasing decisions align with long-term cost savings and fleet efficiency goals.
How Lifecycle Management Drives Smarter Fleet Decisions
For many fleets, the decision to repair or replace an asset is often reactive—based on guesswork rather than data. Without a comprehensive view of ownership costs over time, it's easy to overspend on aging vehicles or replace equipment too soon, both of which erode profit margins and impact operational readiness.
Pain Point: Unclear Lifecycle Costs & Poor Replacement Timing
When lifecycle costs aren’t tracked properly, fleets may face:
- Excessive Repair Costs: Holding on to high-cost assets increases maintenance expenses and unplanned downtime.
- Premature Replacements: Without tracking TCO, fleets may replace assets too early—wasting capital that could be better used elsewhere.
- Inaccurate Budget Forecasting: Lack of visibility into long-term operating costs makes it difficult to forecast maintenance and replacement needs.
- Underutilized Equipment: Without utilization tracking, some assets sit idle while others are overworked, leading to inefficiencies.
Solution: Total Cost of Ownership (TCO) Insights with Squarerigger
Squarerigger’s Lifecycle Management tools empower fleet managers with:
- Real-Time Cost Visibility: Monitor every cost associated with your fleet—from purchase to retirement.
- Data-Driven Replacement Planning: Use repair frequency, asset utilization, and depreciation data to guide smarter replacement decisions.
- Integrated Financial Tracking: Link asset cost data with work orders, preventive maintenance, and purchasing history to uncover trends and optimize spending.
End Result: Maximize ROI & Minimize Waste
By using Squarerigger’s Lifecycle Management (TCO) solution, fleets can: - Reduce Operating Costs: Identify high-cost assets and act before repair costs spiral.
- Make Informed Investment Decisions: Replace assets at the optimal time based on performance and cost analysis.
- Improve Budget Accuracy: Forecast future maintenance and capital expenses with confidence.
- Extend Asset Lifespan: Track and maintain assets proactively to get the most out of your investment.
Lifecycle Management with Squarerigger gives you the financial clarity and tools to build a leaner, more profitable fleet.
How Lifecycle Management Helps Fleet Operations
Without clear visibility into total cost of ownership, fleets risk overspending on repairs, prematurely retiring assets, or holding onto high-cost vehicles too long. Squarerigger provides the real-time financial insights you need to reduce fleet costs, extend asset life, and plan smarter investments.
Frequently Asked Questions
Have questions? We’ve got answers. See how Squarerigger helps fleets optimize operations, reduce costs, and improve efficiency.
-
Q: Why is tracking total cost of ownership (TCO) important for fleets?
A: TCO analysis helps fleet managers determine when assets should be replaced, how much they cost to operate, and where savings can be made.
-
Q: How does Squarerigger help with fleet replacement planning?
A: Squarerigger tracks repair frequency, depreciation, and operating costs, providing insights into when an asset becomes too costly to keep.
-
Q: Can Squarerigger track lifecycle costs for non-vehicle assets?
A: Yes! Squarerigger can track TCO for trailers, equipment, and other fleet assets, ensuring all assets are optimized for cost efficiency.
Check Out More of Our Fleet Management Software Features
Lifecycle Management
Squarerigger’s Lifecycle Management (TCO) solution helps fleets make smarter financial and operational decisions by analyzing costs, tracking asset health, and predicting optimal replacement timelines.
Read MoreAsset Management
Squarerigger’s Fleet Equipment Management tools provide real-time insights into every vehicle, trailer, and piece of equipment in your fleet.
Read MoreSafety & Compliance
Squarerigger empowers fleets to maintain a culture of safety and compliance with automated inspection scheduling, issue tracking, and documentation management.
Read More